Seit wir der Welt den ersten Prototypen des Sion am 27. Juli 2017 vorgestellt haben, lassen wir euch an der Entwicklung, am Design und natürlich am Bau der nächsten Fahrzeuggenerationen Teil haben. Während der Prototypen-Phase haben wir immer wieder euer Feedback und eure Meinung eingeholt – sei es bei Probefahrten, durch Umfragen oder bei einer Car Clinic. Diese wichtige Phase ist seit März abgeschlossen. Inzwischen stecken wir mitten in einem der spannendsten Momente der Fahrzeugentwicklung: die Fertigung der Serien-Validierungsfahrzeuge.
Unterstützt werden wir dabei von thyssenkrupp und Bertrandt, zwei sehr erfahrene Partner, die nicht nur umfassende Expertise im Bereich Automotive-Engineering haben, sondern auch die notwendige Infrastruktur und Kapazitäten, um die Serien-Validierungsfahrzeuge schnell und qualitativ hochwertig zu fertigen.
Da wir euch auch im Jahr 2020 Einblicke in den Bau unserer SVC2-Prototypen gegeben haben, wollen wir euch natürlich bei diesem wichtigen und einmaligen Prozess nicht außen vor lassen. Auf unseren Social Media-Kanälen gab es schon immer mal wieder einige Fotos und Infos aus der Fertigung zu sehen, heute haben wir uns aber einmal den doch sehr wichtigen Fragen gewidmet, die vielleicht besonders für Laien interessant ist: Was passiert denn da eigentlich genau? Wie wird so ein Serien-Validierungsfahrzeug zusammengebaut? Und wie geht’s dann weiter? Wir haben das für euch einmal zu digitalem Papier gebracht.
Alles beginnt mit der Rohkarosserie
Als Experte für integrierte Karosseriebaulösungen ist thyssenkrupp Automotive Body Solutions für die Produktion des Aluminium Space Frames zuständig. Im zweiten Schritt übernimmt Bertrandt die Montage der neuen Sion-Testflotte hier in München. thyssenkrupp fertigt zunächst die sogenannten Body-in-white, also die Rohkarosserie der Fahrzeuge. Dafür werden alle benötigten Aluminium-Profile, Bleche und alle sonst noch benötigten Aluminium-Kleinteile gefertigt und im nächsten Schritt miteinander verbunden.

Bereits vor der Montage bei Bertrand bekommt der Aluminum Space Frame eine KTL-Beschichtung. “KTL” steht für Kathodische Tauchlackierung, ein lange haltbarer Korrosionsschutz. Später wird der Space Frame dann mit unseren Solar Body Panels verkleidet. Hier lautet unser Motto: Solar statt Lack!
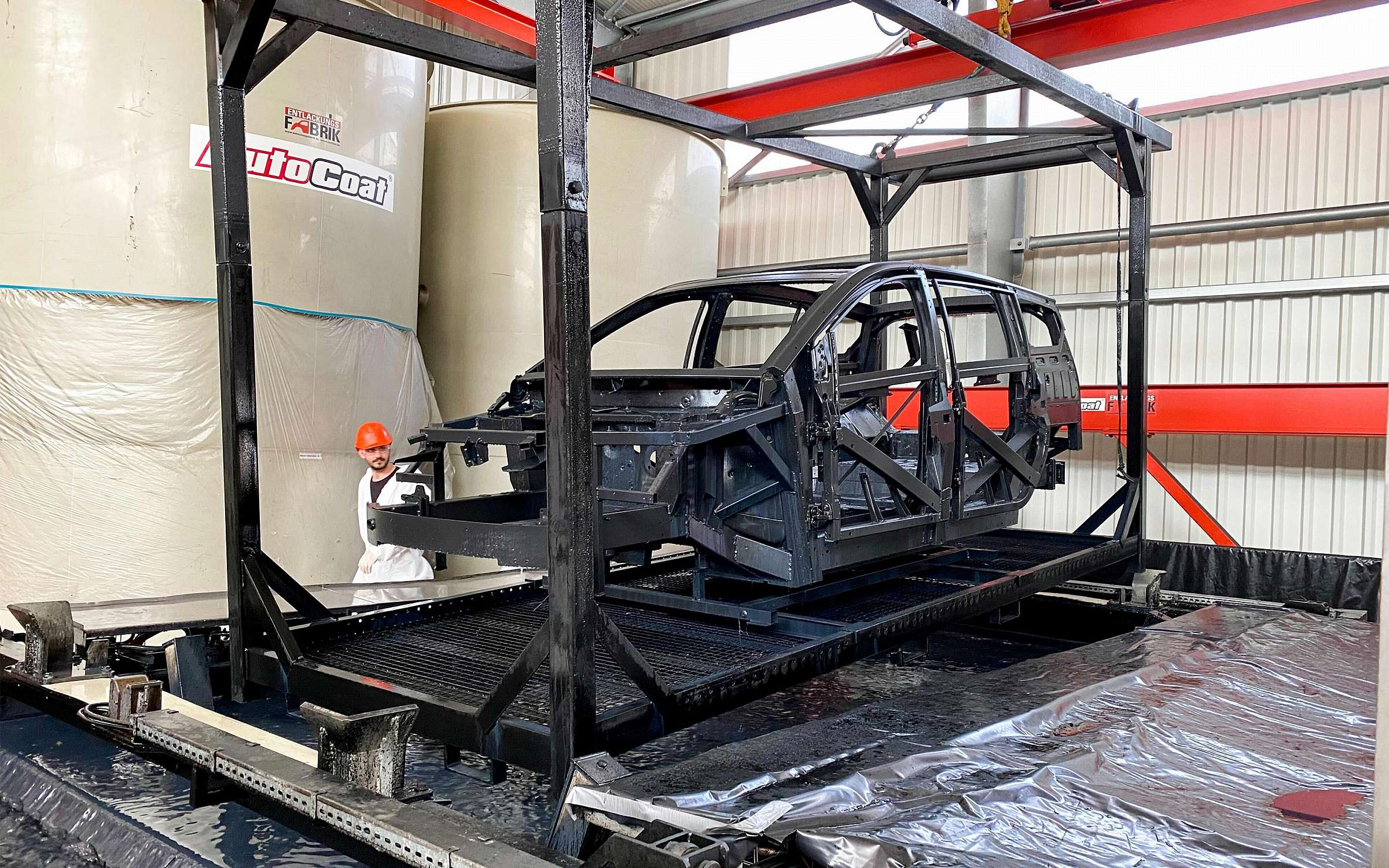
Lasst die Montage beginnen
Insgesamt besteht der Sion aus über 1.500 Teilen, welche in der Endmontage zusammengeführt werden müssen. Hier zeigt sich auch, ob und wenn ja welche Anpassungen in der Konstruktion vor der Serienfertigung noch vorgenommen werden müssen.
Der Body-in-white verfügt über eine VIN-Nummer, die Vehicle-Identification-Number. Sie begleitet das Fahrzeug von der Montage, über den gesamten Lebenszyklus und ist ein wichtiges Identifikationsmerkmal für jedes Fahrzeug. Viele der nun folgenden Schritte laufen parallel, bevor sie zu einem späteren Zeitpunkt zusammen laufen.
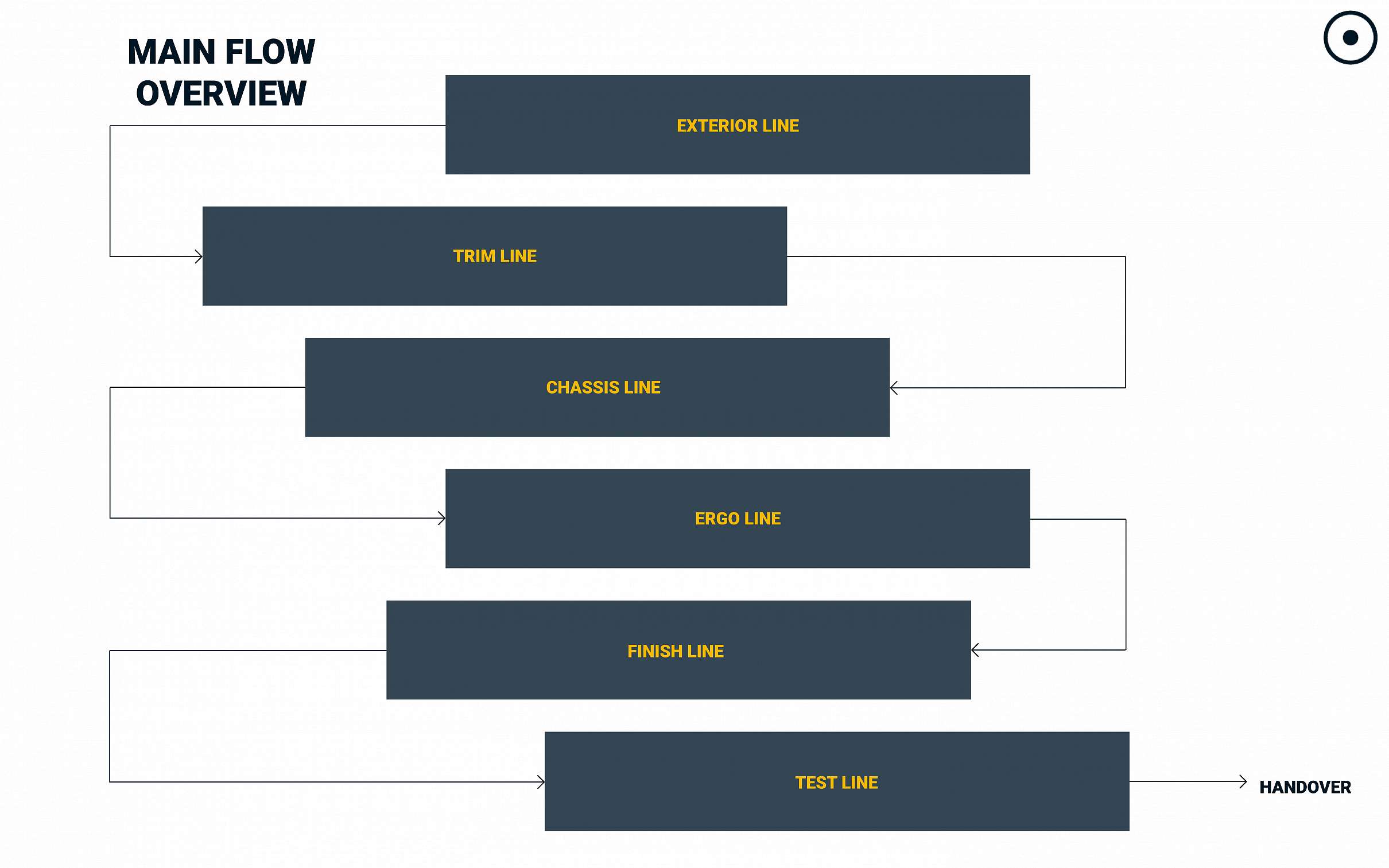
Die Montage startet, indem alle beweglichen Komponenten der Rohkarosserie, nämlich Türen, Motorhaube und Heckklappe von der Karosserie entfernt und auf eigens dafür vorbereitete Vormontagebereiche verlagert werden. Dort erhalten sie die Solar-Integration, die elektrische Integration, die Verkleidung, die Dämmung und die notwendigen Schalter.
Beim Zusammenbau all dieser Komponenten zeigt sich, wo sich für die Serie noch notwendige Verbesserungen ergeben, die dann in die Serienproduktion überführt werden müssen. Die Montagelinie des Exterieurs bildet die führende Montagelinie, auf der alle Komponenten schrittweise zusammengeführt werden.
Im Body-in-white wird in diesem Prozess simultan auch der sogenannte Wiring Harness, der Kabelbaum, verlegt. Der Kabelbaum ist das zentrale Nervensystem der elektrischen Architektur des Fahrzeuges und verbindet alle elektrischen Komponenten miteinander. Ihre Funktionalität wird vor der Integration in das Fahrzeug auf einem Yellow Board geprüft. Dort testen die Ingenieur:innen ob alles korrekt gefertigt wurde. Bei den tausenden von Kabeln kann es vorkommen, dass sich kleine Fehler einschleichen. Diese müssen vor der Integration in das Fahrzeug natürlich behoben werden. Erst dann werden Blinker, Warnleuchten, sämtliche Lichter und alle dazugehörigen Schalter in ihrer Funktion abgenommen.
Nach der Integration des Kabelbaums folgt die Montage des Interieurs. In vielen verschiedenen Schritten werden nun Mittelkonsole, Teppiche, Himmel, Sitze, Innenverkleidung, wie auch das Armaturenbrett im Fahrzeug integriert. Das Armaturenbrett wird ebenfalls in einem eigenen Montagebereich zusammengesetzt und als Einheit in das Fahrzeug integriert und montiert. Die Schwerpunkte bilden hier die Luftkanäle, das Instrument-Cluster, das Infotainment und natürlich das Moos.
Ohne Antrieb kein Vortrieb
Ohne das Herzstück eines jeden Autos tut sich natürlich nichts: der Antrieb. Auf der dafür vorgesehen Montagefläche für das Fahrgestell des Sion, werden verschiedene schwere Komponenten zusammengeführt. Das Fahrwerk ist ein komplexer Verbund bestehend aus Federn, Dämpfern, sowie Felgen mit Reifen, Gummilagern, der Lenkung, Stabilisatoren und den Bremsen. Im vorderen Bereich des Unterbodens liegt der elektrische Motor. In einer extra dafür vorgesehen massiven Halterung wird er fest montiert. An dieser Stelle wird sich später der elektrische Vortrieb auf die Vorderachse übertragen.
Auch das bidirektionale Ladegerät wird im vorderen Teil des Fahrzeuges montiert und ermöglicht zu einem späteren Zeitpunkt unter anderem das Laden der Batterie. Die wohl schwerste Komponente ist die Hochvoltbatterie – sie befindet sich zwischen der Vorder- und Hinterachse. Auch diese Komponente wird auf einem dafür vorgesehenen Montagebereich montiert. Dabei ist nicht nur höchste Konzentration gefragt, sondern auch die Unterstützung von mehreren Hebevorrichtungen. So eine Batterie wiegt immerhin etwa 360 kg.
Im nächsten Schritt werden die verschiedenen Komponenten den Fahrgestells, also die Achsen, die E-Maschine und der Antriebsstrang, an die Karosserie montiert und mit ihr zusammengeführt – der wohl wichtigste Schritt in der komplexen Montage des Validierungsfahrzeugs. Auf der Zielgeraden werden dann Heckklappe, Türen und Motorhaube aus den Montagebereichen wieder am Fahrzeug angebracht. Damit das Fahrzeug während des gesamten Prozesses immer frei zugänglich ist, passiert dieser Schritt ganz am Schluss.
Und jetzt?
Die Montage der Serien-Validierungsfahrzeuge mit über 1.500 Teilen ist dann zwar abgeschlossen, der Prozess der Fahrzeugfertigung allerdings noch nicht. In einem letzten, aber sehr wichtigen Schritt erfolgt die sogenannte Kommissionierungsphase. Dann werden die Fahrzeug zum ersten Mal zum Leben erweckt. Die elektrischen Systeme werden aktiviert und die Steuergeräte mit der Software “geflasht”. Alle Steuergeräte sowie alle elektrischen Komponenten werden dann schrittweise auf ihre Funktionalität überprüft und abgenommen.
Dann zeigt sich die intensive Entwicklungsarbeit von ihrer schönsten Seite. Etwas, dass so noch nie vorher zusammengebaut wurde, erstrahlt in seiner fertigen Form und lässt sich erstmals bewegen.
Die Montage ist ein intensiver und hochkomplexer Prozess, an dem insgesamt hunderte Leute beteiligt sind – sei es in der Vorbereitung, im Bereich Forschung und Entwicklung, oder in der Fertigung selbst. Wir möchten uns an dieser Stelle auch für die großartige Arbeit all der Menschen bedanken, die diesen großen und wichtigen Schritt auf dem Weg in die Serienfertigung des Sion ermöglichen.
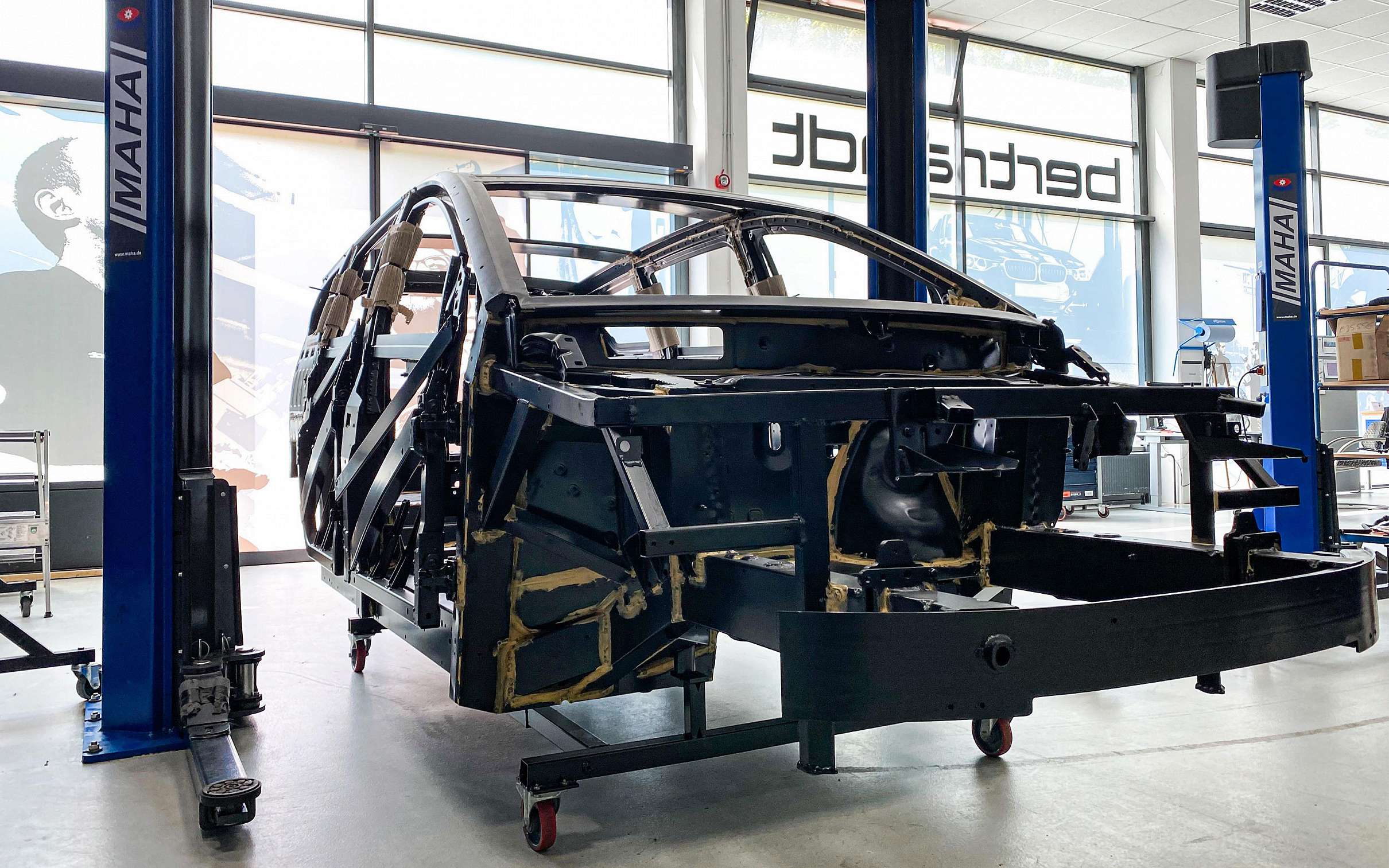
Über die kommenden Wochen und Monate werden wir insgesamt 16 Gesamtfahrzeuge und 21 Versuchsträger anfertigen. Damit erproben, validieren und zertifizieren wir den Sion bevor er im kommenden Jahr dann zum ersten Mal in Finnland vom Band laufen kann. Diese Testwagen absolvieren dabei kompromisslose Praxistests unter extremen Bedingungen. Dazu zählt die Erprobung in verschiedenen Klimazonen, die Optimierung der Solar-Technologie, die Absicherung plus Abstimmung der Fahrdynamik auf Teststrecken und im Straßenverkehr sowie Crashtests. Uns steht also weiterhin eine mehr als spannende Reise bevor, auf die wir euch natürlich hier und auf unseren Social Media-Kanälen mitnehmen möchten. Schaut also immer mal wieder rein, es lohnt sich!
P.S. Die ersten Solar Panels für unsere Serien-Validierungsfahrzeuge sind eingetroffen. Ingenieur Dominik und Community-Vertreter Sebastian sprechen über Beschaffenheit und Materialien sowie über die Herausforderungen, denen wir uns bei der Entwicklung gestellt haben. Spannend: Insgesamt konnten wir mehr Zellen unterbringen als zuvor. Wie genau wir das geschafft haben, erfahrt ihr in diesem Video.